راهنمای کامل تولید کمپوست قارچ دکمه ای به روش بلند مدت
مواد مورد نیاز در تهیه کمپوست قارچ دکمه ای عبارتند از:
1- کاه و کلش گندم 2- کودمرغی 3-گچ هیدراته(پودر سنگ گچ) 4- ملاس چغندرقند 5- کود اوره
توضیح: بعضی از کارخانجات ممکن است مکمل ها افزودنی های دیگری نیز مانند پودر پنبه دانه و پودر سویا برای افزایش پروتئین کمپوست به فرمول کمپوست اضافه نمایند ویا در برخی فرمول ها ملاس و اوره ذکر نشده باشد اما فرمول جامع و کلی در شرایط کشور ما فرمول فوق می باشد و سایر جزئیات و افزودنی ها به این روش در اثر تجربه افراد تغییر میکند.
درصد اختلاط مواد:
1- مقدار کاه و کلش مصرفی در حدود 40درصد وزن کمپوست حاصله می باشد یعنی اگر 10 تن کمپوست بخواهیم تولید کنیم به 4تن کلش نیاز خواهیم داشت.
2- مقدار کود مرغی موردنیاز 60تا 80 درصد میزان کلش مصرفی(برای 4تن کلش در حدود 2500تا 3000کیلوگرم کود مرغی. هر چقدر کود بیشتری مصرف کنیم ، پودر سنگ گچ بیشتری نیز مصرف می کنیم.)
3- میزان سنگ گچ معادل 10تا15 درصد وزن کلش خام. (سنگ گچ تنظیم اسیدیته کمپوست را برعهده دارد و از چسبندگی و لزج شدن کلش جلوگیری میکند. مقداری اضافی مصرف نمودن پودر سنگ گچ مشکلی ایجاد نمی کند ولی کاهش مصرف آن باعث ایجاد اختلال در امر کمپوست سازی می شود.)
4- میزان ملاس و اوره نیز به ازای هرتن کلش خام به ترتیب درحدود 20 و 15 کیلوگرم می باشد.
نکات مهم:
خصوصیات کلش گندم مصرفی :
1) از کلش گندم آبی استفاده شود. ( به دلیل خشبی بودنش)
2) ساقه گندم (کلش) هر چقدر ضخیم تر باشد بهتر است.
3) طول کلش مصرفی 20 تا 30 سانتی متر باشد.
4) پرس های کلش آب نخورده باشد .( زیرا اولا مقداری آب توسط کلش جذب شده و قیمت آن بیشتر می شود. ثانیا احتمال بروز انواع کپک به خصوص کپک سیاه زیاد می شود.)
5) کلش مصرفی ناخالصی نداشته باشد. ( ناخالصی ها عبارتند از : خاک ، مدفوع حیوانات ، ساقه علفهای هرز چند ساله )
مشخصات کود مصرفی :
1) از کود مرغ گوشتی استفاده می کنیم زیرا اولا در جیره غذایی مرغان گوشتی پروتئین بیشتری وجود دارد. ثانیا میزان رطوبت کود مرغ گوشتی کمتر از رطوبت مرغ تخم گذار می باشد.
2) رطوبت کود مصرفی 20 الی 25 درصد باشد.
3) رنگ کود مصرفی روشن باشد . (رنگ کود تازه نوک مدادی روشن است )
4) کود مرغی نسوخته باشد ( فعالیت میکروارگانیسم ها در آن در حد کمی بوده تا مواد غذایی آن از بین نرود. به طور کلی عمر انبار داری کود مصرفی کمتر از دو ماه باشد.)
5) در داخل کود ، کودهای به هم چسبیده (توده ای) نباشد در غیر این صورت خرد شود و سرند شود .
6) کود مصرفی ناخالصی نداشته و میزان ازت آن 3.5 الی 5 درصد باشد.
7) کود مصرفی حتما مخلوطی از کود مرغی و سبوس باشد.
(استفاده از کود مرغ شمال که دارای مقدار زیادی سبوس برنج است)
8) چون منبع انواع میکروارگانیسم های مفید جهت کمپوست سازی کود مرغی می باشد . اگر کود از مرغداری خریداری شود که در جیره غذایی مرغان خود آنتی بیوتیک کمتری مصرف کرده باشد ، بسیار عالی است.
شروع فرآیند فاز یک کمپوست سازی:
1) عمل پیش خیساندن کلش گندم:
بهترین روش جهت عمل پیش خیساندن کلش گندم غرقاب نمودن آن در داخل استخر ساخته شده به همین منظور می باشد.استخر پریوتینگ: این استخر به عمق ۱متر به طوری ساخته می شود که لودر به راحتی وارد آن شود وکلش ها را زیر و رو کند. پرس کلش ها را از هم باز می کنند و در استخر پیش نم می ریزند.ارتفاع آب درون استخر در حدود۲۰تا۴۰ سانتی متر می باشد. بهتر است آب این استخر از آب کثیف استفاده شده در عملیات کمپوست سازی قبلی تامین شود.
آب کثیف : همان هرز آب جمع آوری شده از توده کمپوست می باشد.رنگ آن تیره بوده و حاوی انواع میکروارگانسیم های مفید و مواد غذایی شسته شده از توده کمپوست می باشد.
سپس کلش ها توسط لودر ویا توسط کارگروچهارشاخ کاملا به هم می خورد وتوسط آب چاله کودسازی خیس می شوند. عمل همزدن کلش دو بار انجام می گیرد و در روز سوم کلش ها را روی پیست تخلیه می کنند. جهت شروع کمپوست سازی کلش گندم باید حداقل 75 درصد رطوبت جذب نماید. رابطه مدت زمان عمل پیش خیساندن کلش گندم با مدت انبار داری آن رابطه ای معکوس می باشد. به این دلیل که که در داخل بافت کلش یک سری مواد واکسی ( روغنی) وجود دارد. این مواد آب گریز بوده و سرعت جذب آب توسط کلش را کاهش می دهد. اگر کلش را در انبار نگهداری کنیم ، با گذشت زمان مواد واکسی تجزیه شده و از بین می رود. در نتیجه کلش با سرعت بیشتری آب جذب کرده و مدت زمان عمل پیش خیساندن آن کاهش می یابد.
همچنین برخی کارخانه ها بجای استفاده از استخر پریوتینگ بسته های کلش را از هم باز می کنند و بر روی یک بستری که بتون که دارای زه کش می باشد می ریزند با شلنگ روی آن اب می پاشند و آب خارج شده از زه کش را دوباره روی آن پمپ می کنند (آب کثیف) در ابتدا کلش به سختی آب جذب می کند به ازای هر تن کلش حدود ۵۰۰۰ لیتر آب لازم داریم.
شرح میکس مواد:
کلش آماده شده از مرحله قبل به ارتفاع 40 تا 50 سانتی متر ( به طور تجربی تا زانوی پا ) بر روی پیست کمپوست سازی پخش می کنند. کف پیست بایستی از جنس بتون و زه کشی شده باشد. سپس کلیه مواد دیگر به جز سنگ گچ را بر روی آن پخش می کنیم. توده را به خوبی به هم زده تا ذرات کود به طور یکنواخت بر روی کلش پخش شود.
عمل میکس مواد در حالت دستی توسط کارگر و چهار شاخ و در حالت مکانیزه توسط لودر انجام می شود. توده حاصله را به شکل گنبدی (پایل) دپو می کنند که به آن توده شل و به روز تشکیل توده شل ، روز صفر کمپوست سازی می گویند. بهتر است که در این روز با آب پاشی مجدد نقاطی از توده را که خشک هستند، خیس کرد. این امر به ویژه برای کود مرغی که معمولاً خشک است ضروری است
پس از روز صفر کمپوست را در روزهای دوم ، چهارم ، ششم و هشتم زیر و رو می کنیم و خوب به هم می زنیم. و دوباره به شکل گنبدی دپو می کنیم . این عمل باعث هوادهی کمپوست و یکنواختی عمل تخمیر در کل توده می شود. از روز صفر کمپوست سازی تا روز میک آپ جهت تامین رطوبت از دست رفته کمپوست از آب کثیف استفاده می کنیم . اگر مقدار آب کثیف کفایت نکرد در این مرحله نیز می توان از آب تمیز استفاده نمود. (نباید رطوبت کمپوست کمتر از 70درصد بشود)
پدیده دود کشی :
هوای تازه حاوی اکسیژن از بقل های توده کمپوست وارد آن شده و از مرکز بالایی آن خارج می شود. این جریان هوا ، پدیده دود کشی گفته می شود. این جریان بر اثر اختلاف دمای مرکز کمپوست و محیط پیرامون آن بوجود می آید. در فصول سرد سال به علت اختلاف زیاد دمای گفته شده این جریان با شدت بیشتری انجام می شود و به این ترتیب احتمال بی هوازی شدن واکنش های کمپوست بوجود نمی آید.ولی در فصول گرم سال به علت کاهش اختلاف دمای گفته شده شدت جریان کاهش یافته ، احتمال بی هوازی شدن واکنش های کمپوست بوجود می آید. جهت رفع این عیب در فصول گرم سال نسبت به فصول سرد سال توده کمپوست با عرض و ارتفاع کمتر قالب زنی می شود. این توده حداکثر دارای ابعاد طول و عرض و ارتفاع 1.8 متر می باشد.
چنانچه عمل کمپوست سازی که با انباشتن توده های مرطوب کاه وکلش بر روی هم آغاز میشود به طور مناسب صورت گیرد، درجه حرارت درون توده کمپوست در اثر تخمیر هوازی ناشی از فعالیت باکتری ها و دیگر میکروارگانیسمها بتدریج افزایش مییابد. لذا در سومین روز پس از انباشتن توده کمپوست (شامل تمامی مواد فرمول انتخاب شده است بغیر از سنگ گچ و حشره کشها) ، درجه حرارت مرکز توده کمپوست به 70 تا 74 درجه سانتیگراد میرسد. به این ترتیب، جمعیت میکروارگانیسم های حرارت دوست یا مقاوم بحرارت افزایش مییابد و لذا حرارت زیادی ایجاد میشود. پس از افزایش جمعیت اکتینومایست های گرمادوست، عمل تخمیر ادامه یافته و جایگزین باکتریها و قارچها میشوند و در نتیجه این حرارت اغلب پاتوژن ها و آفات مضر از بین میروند. از آنجا که ارگانیسم های تخمیر کننده، هوازی بوده و به آب و اکسیژن زیادی نیاز دارند، به توده کمپوست مرتباً آب اضافه شده و برای افزایش اکسیژن درون توده عمل برگرداندن توده را انجام می دهیم. کمبود رطوبت باعث اختلال در عمل میکروارگانیسمها شده و ازدیاد رطوبت باعث کاهش اکسیژن توده کمپوست شده، موجب تخمیر بی هوازی و ایجاد بوی بد در کمپوست میشود که در چنین کمپوستی بذر قارچ نمیتواند بخوبی رشد کند.
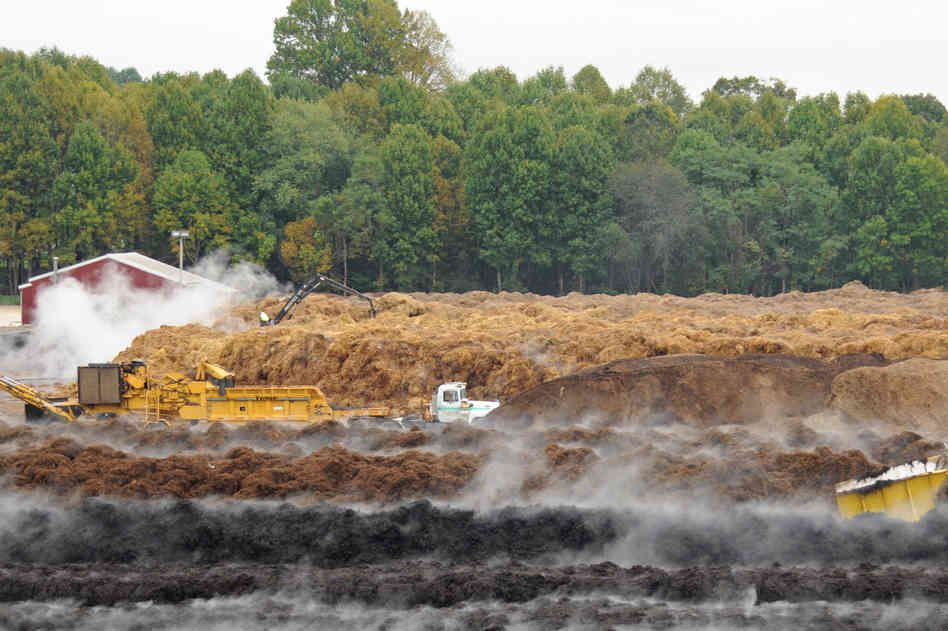
مرحله میک آپ(Make Up) :
روز دهم پس از روز صفر کمپوست سازی ، روز میک آپ نامیده میشود در این روز پودر سنگ گچ به توده کمپوست اضافه شده و توده کمپوست از شکل گنبدی به شکل مکعب مستطیل آرایش می شود. که به این عمل قالب زنی می گویند.
پس از روز میک آپ در روز های 12 ، 14 و 15 قالب کمپوست را مجددا قالب زنی می کنیم. از روز میک آپ (Make Up) جهت تامین رطوبت از دست رفته کمپوست از آب تمیز استفاده می کنیم.
قالب زنی باید طوری انجام شود که به هدف خود یعنی فراهم کردن گرمای مناسب جهت شروع وتحریک و تشدید فعالیتهای تخمیر میکروبی دست یابد. بنابراین ابعاد قالب مهم است. عرض یک قالب باید در شرایط آب و هوایی گرم کمتر و در شرایط آب و هوایی سرد بیشتر باشد. اما معمولاً عرض یک قالب را در حدود یک متر تا دو متر و ارتفاع آن را ۲/۱ تا ۵/۱ متر در نظر می گیرند. در انتخاب طول قالب محدودیتی وجود ندارد.
در هنگامیکه قالب را به هم می زنیم، در نقاطی که لزجی و به هم چسبیدگی کاه وکلش دیده می شود، از مقداری سولفات کلسیم هیدراته یا همان گچ کوره نرفته (پودر سنگ گچ) استفاده شود.
نکته مهم: در هیچیک از مراحل فاز یک دمای توده نباید بالاتر از 75درجه سانتیگراد فراتر برود در غیر اینصورت مواد غذایی مورد نیاز و مفید در توده کمپوست سوخته و از بین خواهند رفت همچنین این دما نبایستی کمتر از 40درجه بشود.
معیار های استاندارد پایان فاز 1 کمپوست سازی :
1) معیار های فیزیکی :
رنگ: رنگ کلش کمپوست از طلایی به قهوه ای تیره تبدیل می شود.
بو: بوی شدید آمونیاک به مشام می رسد.
سختی: اگر مقداری از کلش کمپوست را برداشته و با دو دست از یکدیگر جدا کنیم مقداری مقاومت احساس می کنیم . زیرا مراحل کمپوست سازی تمام نشده و کلش کمپوست کاملا پوسیده و هوموس نشده است.
2) معیار های شیمیایی:
میزان رطوبت (72 - 75 %)
میزان ازت (1.7 - 1.9 %) به ازای وزن خشک مواد
میزان آمونیاک (0/15 %)
نسبت کربن به ازت (C/N) = (20 - 22 )
اسیدیته PH: 8.5
در روز 16 پس از انجام آزمایشات مربوطه کمپوست را جهت طی نمودن مراحل فاز 2 کمپوست سازی به تونل پاستوریزاسیون منتقل می کنیم.
مراحل فاز2 :
1) لول کردن: یعنی هم سو و یکسان نمودن دمای نقاط مختلف کمپوست در داخل تونل پاستوریزاسیون .
این مرحله در دمای 45 - 50 انجام می شود. کمترین و بیشترین زمان انجام این مرحله در کارخانه ملارد 5 - 12 ساعت
می باشد.
2) میت آپ : در این مرحله مقداری بخار آب به توده کمپوست تزریق می کنیم تا فعال شده و دمای آن افزایش یابد. افزایش دما در این مرحله تدریجی بوده و به ازای هر ساعت 1 - 1.5 درجه سانتی گراد می باشد. تا به دمای 58- 59 درجه سانتی گراد برسد.
دلیل افزایش تدریجی دما در این مرحله عبارتند از :
الف) عدم ایجاد استرس دمایی در میکروارگانیسم های مفید.
ب) کنترل راحت افزایش دما و توقف دما در 58 - 59 درجه سانتی گراد.
3) پاستوریزاسیون : در دمای 58 - 59 درجه سانتی گراد و مدت 8 الی 10 ساعت پاستوریزه می شود.
اهداف پاستوریزاسیون :
الف) هضم انواع عوامل بیماری زا (پاتوژن ها) و آفات
ب) فعال نمودن میکروارگانیسم های گرما دوست (ترموفیل)
نکته: در دمای کمتر از 57 درجه سانتیگراد عمل پاستوریزه به خوبی انجام نمی شود و تعدادی از میکرو ارگانیسم های غیر مفید باقی می مانند و در دمای بالاتر از 60 درجه سانتیگراد میکرو ارگانیسم های مفید از بین می روند .
4) سرد کردن اولیه : در این مرحله دمای کمپوست را به ازای هر ساعت 1- 1.5 کاهش می یابد تا به دمای 47- 48 درجه سانتی گراد برسد.
5) شیرین کردن : این مرحله در دمای 47- 48 درجه سانتی گراد و مدت تقریبا 5 روز انجام می شود.
در این مرحله میکروارگانیسم های مفید مانند قارچ های گرما دوست و اکتینومیست ها فعال شده و عمل آمونیاک گیری از توده کمپوست انجام می شود. در پایان این مرحله مقدار آمونیاک کمپوست توسط وسیله ای بنام دراگرتیوپ از هوای کانال برگشتی تونل اندازه گیری می شود.اگر میزان آمونیاک 30ppm یا کمتر باشد. می توان مرحله بعد را انجام داد و در غیر این صورت تا کاهش میزان آمونیاک کمپوست به حداکثر 30 ppm این مرحله ادامه پیدا می کند.
6) سرد کردن جهت بذر زنی :
در این مرحله دمای کمپوست به ازای هر ساعت 3- 4 در جه سانتی گراد کاهش داده تا به دمای 25 درجه سانتی گراد برسد.
سپس کمپوست را از تونل خارج کرده و با اسپان قارچ تلقیح می کنیم و به سالن تولید منتقل می کنیم . تنها روش اضافه کردن اسپان قارچ به کمپوست در ایران روش مخلوط بوده و جهت تلقیح هر 1000 کیلوگرم کمپوست ، تقریبا 10 - 12 کیلوگرم اسپان قارچ مصرف می کنیم.
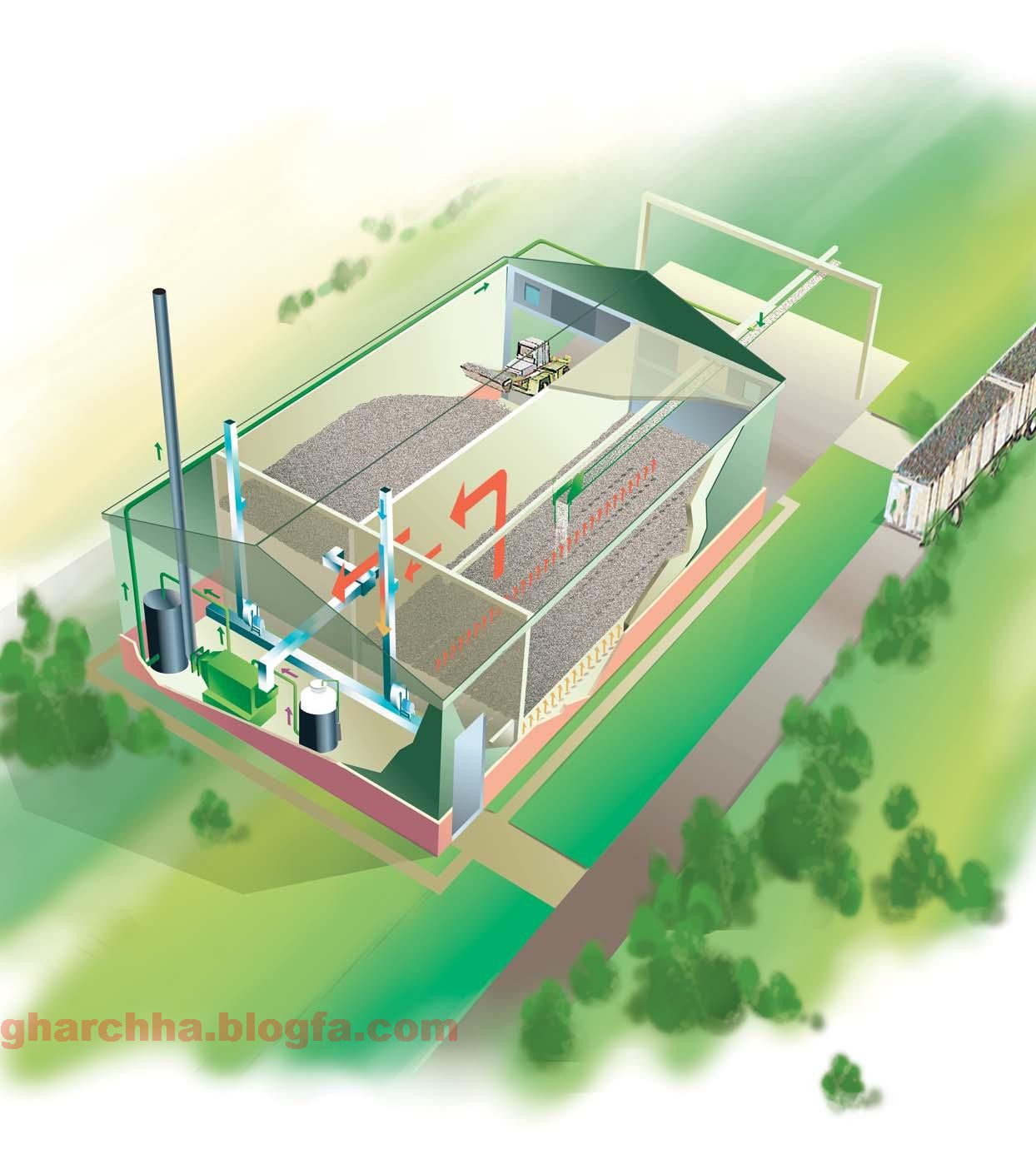
نکات پایانی:
اگر مرحله آمونیاک گیری به نحوه احسن انجام نشود مشکلات زیر بوجود می آید:
الف) اسپان قارچ به مقادیر ناچیز آمونیاک (حتی 20 ppm) حساس بوده و در حضور آمونیاک از بین می رود. در نتیجه محصول تولید نمی شود.
ب) در کمپوست حاوی آمونیاک قارچ هرز یا رقیب کلاهک دارای از خانواده کاپریموس (کلاهک) یا (کلاهک جوهری) رشد می کند. این قارچ از نظر سازگاری با شرایط محیطی و جذب مواد غذایی بر قارچ خوراکی ما ، برتری داشته و سریعا در بستر مستقر می شود.
فایر فنگ (نیش آتشین ) : بقایای میکروارگانیسم های مرحله آمونیاک گیری پس از خارج نمودن کمپوست از تونل پاستوریزاسیون به شکل لکه های سفید مایل به خاکستری بر روی کلش کمپوست با چشم غیر مسلح به راحتی دیده می شود. که به آن فایرفنگ یا نیش آتشین می گویند.
معیارهای استاندارد پایان دوره 2(فاز دوم) کمپوست سازی:
الف) معیارهای فیزیکی :
1) رنگ : رنگ کلش کمپوست قهوه ای تیره با لکه های سفید مایل به خاکستری (قهوه ای تیره)
2) بو : از کمپوست دیگر بوی آمونیاک به مشام نمی رسد. (کمپوست بوی شیرین علف تازه می دهد)
3) سختی : اگر مقداری از کلش کمپوست را برداشته و با دو دست جدا کنیم ، مقاومتی احساس نمی کنیم زیرا با عنایت به اتمام مراحل کمپوست سازی کلش گندم کاملا پوسیده و هوموس شده است.
4) آزمایش انگشت: مالش کمپوست توسط دو انگشت شصت و سبابه و عدم چسبندگی کمپوست، نشان از کیفیت خوب آن دارد.
ب) معیار های شیمیایی:
1) میزان رطوبت : 68 تا 70 درصد
2) میزان ازت 2.2% به ازای وزن خشک مواد
3) نسبت کربن به ازت C/N : 16
4) اسیدیته PH : 7.5
5) EC : بین 0.5 تا 1 میلی موس.
منبع :
مهندس زارعی
http://gharchha.blogfa.com/post/31